Case Study: Wind Turbine Slip-Ring Debris
Wind turbines have been favored in many areas because of their ability to provide communities with environmentally friendly energy. According to Machinery Lubrication, most wind turbines are reliable 98% of the time. When they do fail, it is often due to failed or non-existent maintenance. Wind turbines can be expensive to operate, and when they need to be serviced, the downtime can prove costly to energy providers. Greases and oils are frequently used in routine maintenance but using the wrong lubricant can sometimes do more harm than good.
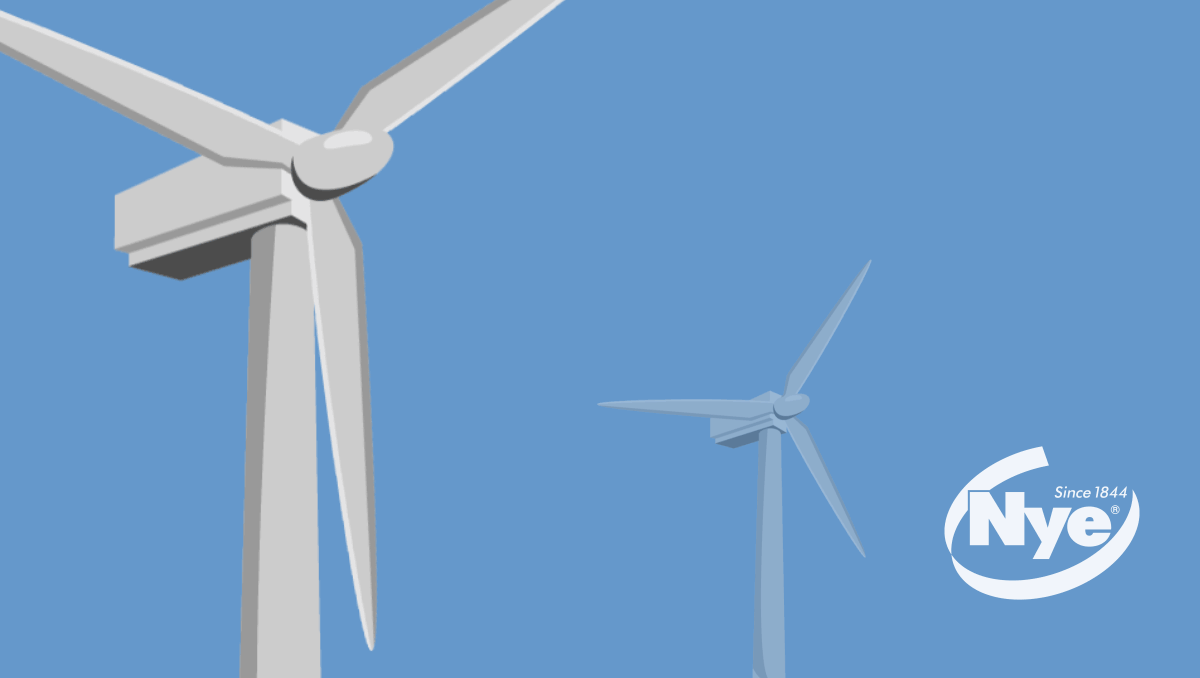
A Messy Problem
A European manufacturer of industrial materials and electrical components contacted Nye regarding a problem they were having with their wind turbine slip rings. The manufacturer had previously been using a competitor lubricant to lubricate the slip rings and the lubricant was causing a black debris to form around the slip rings. The slip-rings, made from gold rings and gold fingers, help to facilitate signal and power connections between the rotating blade shaft and the stationary generator of the wind turbine. Slip-rings ride along as the assembly rotates which means that a lubricant is required in order to protect the metal surfaces and prevent wear. The manufacturer needed Nye to provide a lubricant that would prevent the formation of debris on the slip ring to ensure uninterrupted operation.
Digging Deeper
Upon observation, Nye noticed the lubricant previously used by the manufacturer had been applied with aerosol spray cans. When lubricants are applied with aerosol cans, there is a heightened risk of contamination because once airborne, the lubricant can adhere to nearby surfaces. In this case, the aerosols contaminated the slip rings during assembly.
The Nye Solution
Nye recommended that the manufacturer switch to a PFPE lubricant and adjust their application methods. This involved changing the cleaning solvent used to prepare the slip ring surfaces for the PFPE oil. At our suggestion, they changed from a fluorohexane to a hydro-fluoroether that could remove the hydrocarbon contamination as well as PFPE contamination.
Product | Chemistry | Temp Range (°C) |
Application Notes |
---|---|---|---|
UNIFLOR 8950 | PFPE | -90 to 225 | A light viscosity, completely fluorinated oil possessing very wide temperature capability, excellent oxidation resistance, excellent plastic and elastomer compatibility and resistance to aggressive chemicals. |
After customer testing, the manufacturer decided to go with Uniflor™ 8950, a light viscosity, completely fluorinated oil. This PFPE lubricant is resistant to aggressive chemicals and has a very wide temperature capability of -90 to 225°C. Additionally, Uniflor™ 8950 exhibits excellent oxidation resistance to protect metal components while also being compatible with plastics/elastomers. The right grease reduces the need for maintenance, offering the company significant cost-savings. The customer remains satisfied with our product and has not experienced any slip-ring debris.
Click here to learn more about our lubrication options for power & utility applications.
Jay Weikel – EU Engineering Manager
Jay have been with Nye for 24 years. Prior to his role as the EU Engineering Manager, Jay served as Nye’s Southeast Engineering Manager. Jay specializes in providing lubrication solutions for medical applications and PFPE technology. He holds a Bachelor of Science in Chemical Engineering from North Carolina State University and an MBA from the University of Delaware.
Click here to connect with Jay on LinkedIn.